The distribution warehouse would be storing Wolverine’s inventory before it was sold to Wolverine’s Asian customers, and the inventory would still need to be considered the property of Wolverine until the sales actually occurred. This required a customer consignment inventory approach, whereby the supplier maintains control of inventory that is in the customer’s location until that inventory is actually used.
At A Glance
- ERP from the Plex Smart Manufacturing Platform brings supplier of vibration damping and sealing materials the ability to trace all warehouse inventory that has shipped but not yet sold.
- Wolverine, its warehousing partner in Asia, and its end customers track physical inventory with 100 percent accuracy.
- Integrated functions enable Wolverine to create accounts receivable invoices at the exact time customers use inventory.
- Audit times have been reduced from eight hours to less than one hour a month.
If we hadn’t implemented the Plex consignment inventory module, we would have had to develop a completely manual process where we’d constantly be trading Excel spreadsheets with our warehouse partner.
Wolverine immediately approached Plex Systems, its manufacturing cloud ERP provider, and discovered that the solution lay within the Plex system it was already utilizing.
The addition of a customer consignment function available within Plex has enabled Wolverine to flag and trace all warehouse inventory that has shipped but not yet sold. The liability for loss, damage, obsolescence, and theft automatically remains with Wolverine, and all information is totally visible to Wolverine. All of the inventory data is automatically integrated with sales, shipping, accounts receivable, and scheduling so Wolverine knows the status of all inventory at all times.
Most ERP systems have difficulty with consignment inventory because invoicing is not typically tied to shipments or receipt transactions. Plex, however, was able to provide this functionality seamlessly because all of its functions are integrated.
Since the launch of the customer consignment function, Wolverine has been able to easily create and access accurate inventory reports; eliminate the need for manual inventory processing; easily track shipments and verify customer usage; and foster even stronger relationships with its warehouse business partner and its customers in Asia.
Results
Because the company had already been utilizing Plex ERP for production, purchasing, scheduling, and receiving, it took only two months to customize and launch the customer consignment inventory function.
Almost immediately, Wolverine began to experience the benefits of the new integrated customer consignment processes.
The new process for tracking consignment inventory, for instance, is fairly seamless to the user. When a Wolverine employee enters a customer code to arrange shipment of materials, he or she can select “Consignment Inventory” from the customer menu to identify the affected containers.
For each affected customer code/part number, a Wolverine employee completes a Customer Inventory Setup screen. He or she then enters a customer order, turns on the “In-Transit” flag, and presses the “Ship” button for any consigned product leaving the Wolverine docks. After the customer shipping setup is completed, the inventory containers appear in the consignment function.
Invoices are automatically created by the warehouse partner when the containers are actually consumed. These invoices use the price that is valid at the time of usage, not at the time of shipment.
Not only is the process seamless for Wolverine, but employees of Wolverine’s warehouse partner in Asia have also been enjoying the ease with which they can track consignment inventory. They are able to view the same data as Wolverine so they know when consignment-flagged inventory will arrive, of what part numbers, in what quantities, and for which end-customers they are intended to be sold.
Overall Benefits
The benefits intrinsic to a customer consignment process have been even more pronounced for Wolverine because it selected Plex Systems to provide this functionality as part of the Plex system it already had in place.
All of the functions in Plex are automatically integrated, and the integration of the inventory systems with sales, shipping, accounts receivable, and scheduling has enabled Wolverine to create accounts receivable invoices at the exact time the customers utilize the inventory. This allows Wolverine, its warehousing partner, and its end customers to track physical inventory with 100 percent accuracy from the moment it leaves Wolverine’s U.S. docks through consumption by its customers in Asia.
The Plex function enables Wolverine to maintain accurate inventory tracking without manual processes.
“If we hadn’t implemented the Plex consignment inventory module, we would have had to develop a completely manual process where we’d constantly be trading Excel spreadsheets with our warehouse partner,” explained Manager of Business Applications Theresa Gemus. In addition to this time savings, the ease with which inventory data can now be accessed has enabled Wolverine to reduce its audit time from eight hours a month to less than one hour each month.
The precision of the inventory data is another benefit. Wolverine management is completely confident in the timeliness and accuracy of the cost of sales as shown regularly in the company’s standard cost activity report. Managers can also access an automated Inventory Evaluation Query Report at any time to view the precise value of materials in transit. This, in turn, enables them to track cash flow and profitability with no margin of error.
A final, unexpected, benefit of the Plex consignment function is its contribution to Wolverine’s improved relationships with its partner and customers in Asia.
“Our immediate need was to be able to keep track of our in-transit inventory until it is actually sold,” said Gemus, “and, in the process, we’ve given our warehouse partner the ability to better track its inventory too.”
We maintain 100 percent accurate inventory tracking without manual processes.
“Our partner’s employees are very happy not to have to do the manual labor that typically comes with this kind of arrangement. The bonus is they can also plan their operations more effectively, because they’re able to see exactly what materials and products are arriving soon."
About Wolverine Advanced Materials
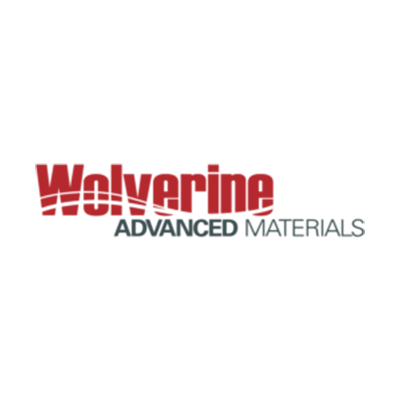
Wolverine Advanced Materials, a global supplier of vibration damping and sealing materials, formed a unique business venture with a warehousing company in China. With this unique venture came a unique challenge in the area of inventory management.
Industry: Automotive
Location: Dearborn, MI
Published September 1, 2020
Featured Resources