For several years, Spring Dynamics had been utilizing an on-premise ERP system that included accounting functions and standard reports on inventory, accounts receivable and accounts payable. Management wanted a more robust, comprehensive system that would also include shop floor operations, generate management reports and help maximize overall business performance.
At A Glance
- A spring manufacturer selects Plex ERP over QAD based on Plex’s more affordable cost, its usability and its popularity among the manufacturer’s customers.
- Discrepancies between recorded and actual inventory decreased from an average of 5 percent to virtually zero.
- More comprehensive tracking of products as they are manufactured improves Spring Dynamics’ inventory management, traceability, and resource forecasting.
- Employees increased their productivity; they now enter data just once in the integrated system and there’s no need for duplication.
We have seen ‘crazy’ improvements in operations, and have not had one single regret about going with Plex.
Plex ERP Selected Over QAD
After one failed (and costly) attempt to launch a system it felt could meet these requirements, Spring Dynamics feared the disruption and capital investment involved in installing another solution. It approached a second review of potential solutions very cautiously. After a lengthy and intense analysis of possible solutions, management narrowed the search down to two candidates: Plex ERP and QAD.
After reviewing demos, talking with existing customers of both products, and meeting with their development and management teams, Spring Dynamics selected Plex. The company preferred Plex to QAD for three reasons:
- Plex appeared to be a lot more user-friendly than QAD.
- There was less of an outlay of cash with Plex.
- Many of Spring Dynamics’ customers had been moving to the Plex Smart Manufacturing Platform, and management saw distinct advantages to using the same system its customers prefer.
“There was only one person on our management team who held out for QAD after our initial review and that was only because he was already familiar with it,” noted Spring Dynamics President Jessica Marco. “Once he saw Plex in action, he was impressed and came around quickly.”
Comprehensive Solution
Plex ERP was launched in both of Spring Dynamics’ facilities simultaneously in just four months.
“We were looking for a solution that would suit what we do on the shop floor,” explained Marco, “and that’s exactly what Plex has done for us.”
Because Plex combines the capabilities of enterprise resource planning (ERP), manufacturing execution systems (MES), quality management, customer relationship management (CRM) and shop-floor integration, it has ideally served Spring Dynamics’ needs for an all-in-one, shop-floor-to-top-floor solution. It enables the company to more effectively and efficiently manage every aspect of its operations.
Also, because it is a cloud-based model, Plex ERP is securely managed and maintained off-premises. Employees access data online and the company does not need to dedicate internal resources to managing the system.
Today, employees are able to access and print real-time reports while filtering out data as needed. The integration of data and the use of common processes enable management to have a more accurate view of the operations in both of the company’s plants at all times. Accurate, comprehensive tracking of products as they are manufactured improves inventory management, traceability, and resource forecasting.
“Since the launch of Plex, we’ve had only miniscule variation in physical inventories."
Inventory Variations Eliminated
Before launching Plex, Spring Dynamics needed to invest internal resources to track down missing products on a weekly basis.
“We had two people in the Materials Department who had to run around and pull cartons, manually enter part numbers, and print and compare paper reports in order to try to figure out what was missing and where it was,” explained Marco.
Now, the company uses barcode labeling and scanning processes to identify and track all products. Everything runs much more smoothly. Inventory is tracked at virtually 100 percent accuracy.
“Before, when we conducted our physical inventories, we’d typically find about a 5 percent variation between actual and recorded inventory,” she continued. “Since the launch of Plex, we’ve had miniscule variation – actually just one tub of parts, once, and that was just an item we forgot to enter prior to the launch of the new system.”
Improved Forecasting
Before Plex Manufacturing ERP, Spring Dynamics prepared, printed, and relied upon many paper Excel spreadsheets each day to manage operations. Plex has eliminated this need.
Employees can access Plex data online and pull customized reports anytime, from anywhere with Internet access, and it only takes a few mouse clicks.
In addition to easier access to data and reduced paper costs, managers are very pleased with the accuracy and detail of the reports they pull from Plex.
“I can trace everything back to the second the raw materials arrived, without ever leaving my desk.”
“For example, the customer release reports are great,” explained Marco. “When I access the customer release screens, I get perfect, accurate data for forecasting.”
“Also, we can now look at inventory to see how old it is. Our previous system only recorded current quantities but not receipt dates or any historical data,” she continued. “You’d have to physically go look at inventory to find out its age.”
Resource Savings
“Everything was ‘very 80s’ before Plex,” said Marco. “Before, every move had to be manually entered and recorded. Now we enter data just once and there’s no duplication or replication. We’ve significantly improved our productivity.”
The transformation from manual to automated tracking not only streamlined and sped operations. After launching Plex ERP, Spring Dynamics was able to eliminate a position. It no longer needed a shipping clerk dedicated to data entry.
Because Plex Manufacturing ERP is a cloud-based solution, all of the company’s data is securely housed and maintained off-site by Plex Systems. Spring Dynamics avoids costly servers, hardware, and energy costs. There’s no need for internal IT maintenance related to materials resource planning (MRP).
The company rests assured that its data is housed in a highly secure environment with back-up servers and industry-leading disaster recovery levels. In addition, enhancements are made to the software on a real-time basis at no additional cost to users; there are never new versions to install.
About Spring Dynamics
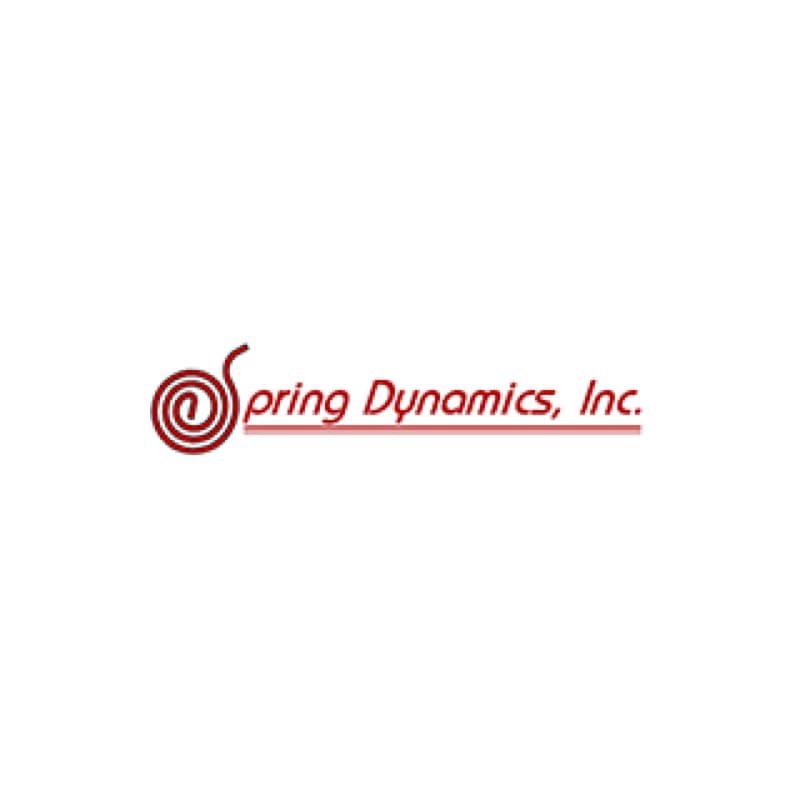
Spring Dynamics, Inc., is a manufacturer of springs primarily for the automotive industry. Headquartered in Almont, Michigan, the company also has a second facility in Harlingen, Texas.
Industry: Manufacturing
Location: Almont, MI
Published October 1, 2011
Featured Resources