Last week I discussed the importance of starting out your quality journey by eliminating manual processes and embracing digitization. For the second blog in this three-part series, let's look at a natural next step for progression that many manufacturers are taking — extending their quality approach beyond their "four walls" and into the supply chain.
Most manufacturers today depend on a global network of suppliers to produce their goods. However, these supply chains bring their own challenges that must be managed effectively, especially regarding quality. An OEM and their suppliers share the responsibility for quality performance ‒ manufacturers must look for ways to engrain the supply chain into their quality approach.
Managing these interactions with suppliers is where successful manufacturers truly stand out. The supplier relationship can be one that varies greatly between companies, with Figure 1 highlighting a maturity level of sorts for how well manufacturing operations work with suppliers.
Figure 1: Operations Approach to Working with Suppliers
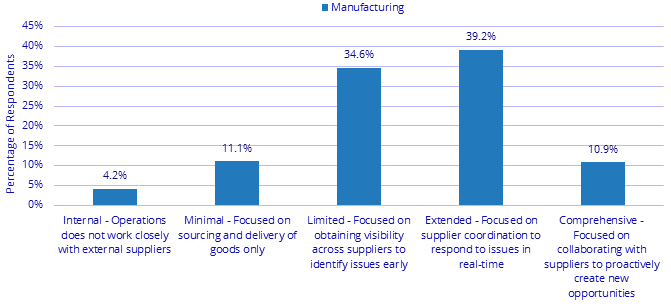
Source: IDC Future Enterprise Resiliency & Spending Survey – February 2021
For the least mature manufacturers, suppliers are seen as necessary speed bumps ‒ third parties that can potentially derail an order with one nonconforming or late shipment. Immature manufacturers look at suppliers as merely that — send me products. Mature manufacturers look at the supply chain and quality as an overall component of their business process and take responsibility. For leading companies, suppliers are viewed as strategic partners for delivering superior quality. For manufacturers just starting out, a good way to begin extending quality into the supply chain is by monitoring supplier metrics and taking a proactive approach. Similar to the plant floor benefits of visibility into performance, the same holds true for supplier quality management – knowing how suppliers perform is essential to make the best choices.
Metrics/areas that can be used to measure supplier performance:
- On-Time Delivery
- Defect Rate
- Product Quality
- Product Cost
- Number of Outstanding Supplier CAPAs
- Charge Backs
- Sustainability Performance
- Compliance to Standard Operating Procedure (SOP)
- Supplier Responsiveness
- Supplier Capacity
- Effectiveness of Supplier Quality Management System
- Ability to Collaborate on Product Design
However, properly managing your suppliers is more than just measuring performance on items such as on-time delivery or defect rates; it's about being proactive and spotting trends before they become issues. The critical capability that manufacturers need to improve in supplier management is real-time visibility into supplier quality performance. Ensure your suppliers offer access to their business through a supplier portal. Real-time visibility allows a manufacturer to discover and fix problems before they escalate, lowering overall costs and ensuring no delays in delivery. Manufacturers without this capability must rely solely on reacting to problems as they arise, which has a severe impact on the cost and quality of their products. Manufacturers that do not take this approach with the supply chain greatly increase risk in the business and to their end customers; this is applicable regardless of the vertical or segment the manufacturer serves.
Only 11% of the industry is in the comprehensive maturity level which focuses on collaborating with suppliers. Manufacturers looking to take this comprehensive approach should focus on how everyone involved can perform better. For example, regular planning sessions can help improve quality performance. With this increased focus on collaboration, ideas to improve are bound to occur, which is a win-win for all parties involved. These manufacturers can better plan their own resources, and suppliers find these companies easier to work with, encouraging lower bids and future business. For companies that are suppliers to large OEMs, the ability to demonstrate superior quality performance will become even more of a differentiator as they push further into their own supply chain with more stringent requirements.
While digitized quality processes and effective supplier quality management are important steps to take, the journey should not end there. The third and final blog in this series will focus on the importance of instilling a quality mindset and culture across your organization so that continuous improvements can be made over time.
Related Articles